Mesin Pelabelan Lem Panas OPP Putar Otomatis
Deskripsi
1.Kebutuhan Klien
Nomor |
Isi |
Persyaratan |
1 |
Bahan produk/bentuk |
PET/botol bulat |
2 |
Spesifikasi produk/ukuran |
|
3 |
Posisi label |
tubuh botol |
4 |
Jumlah label |
1 |
5 |
Bahan label |
tidak tembus cahaya Transparan |
6 |
Ukuran label |
|
7 |
posisi instalasi |
Pengisian rafter sebelum pengisian |
8 |
kapasitas |
12000-15000 BPH |
2.Model Rekomendasi
Mesin Pemberi Label Lem Panas OPP Putar Otomatis RYRH-812V-2
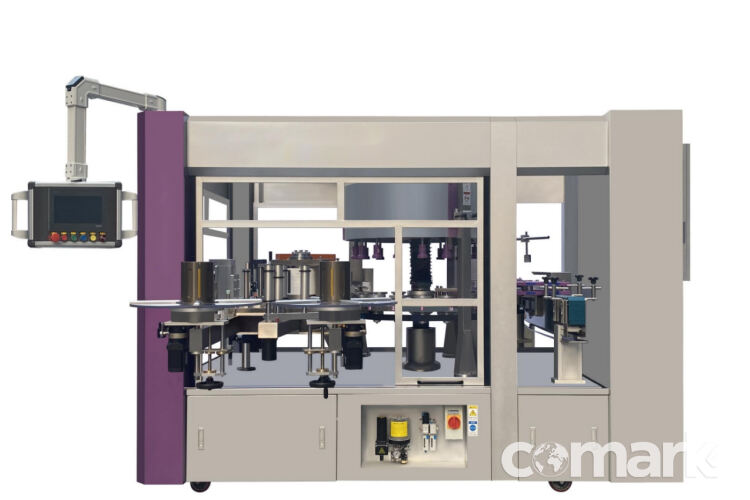
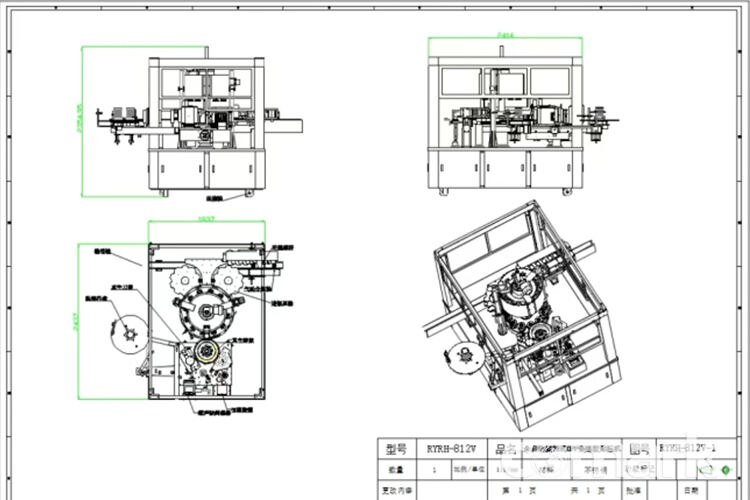
3.Komponen Perangkat
5.1 Konfigurasi Dasar dan Merek Komponen Listrik
Motor servo: sistem motor servo ABB berdaya tinggi dan inersia tinggi
Driver servo: sistem penggerak sinkron ABB
PLC: BECKHOFF dari Jerman
Antarmuka manusia-mesin: layar warna Schneider berukuran 10 inci
Sensor kode warna: sensor label kode warna SICK dari Jerman, mendeteksi tanda warna tertentu pada label
Sensor produk: sakelar fotoelektrik deteksi kecepatan tinggi SICK
Motor utama: Siemens
Inverter frekuensi: DANFOSS
Perangkat koreksi: TECHMACH
Komponen tegangan rendah: FESTO, Schneider
Komponen pneumatik: FESTO, MAC, kipas bertekanan tinggi Taiwan
Encoder: encoder SICK berkecepatan tinggi dan presisi tinggi
Perangkat lem panas: kotak lem yang dikembangkan secara mandiri
Sistem pengulangan:Maxcesssistem pengulangan bubuk magnetik dari Amerika Serikat yang menjamin stabilitas dan ketegangan konstan saat pengulangan
Sistem pelumasan mesin keseluruhan: sistem pengisian minyak otomatis impor dari Korea Selatan
5.2 Penyangga: Baja tahan karat, roda kastor universal, baut penahan
5.3 Poros: Bahan utama yang digunakan adalah aluminium cor dan baja tahan karat cor, dan poros inti terbuat dari 40Cr berkinerja tinggi
5.4 Sistem konveyor: Seluruh sistem menggunakan lebar rantai standar, yang memungkinkan penyambungan yang lebih fleksibel;
5.5 Rangkaian roda bintang: transfer produk yang halus pada jalur konveyor ke poros
5.6 Sistem penyesuaian ketinggian stasiun: fleksibel untuk membungkus botol pada ketinggian yang berbeda
5.7 Sistem stasiun pemberian label: sistem pemberian label yang mengintegrasikan pelepasan gulungan, pemberian label, pemotongan label, perekatan, dan penekanan label
5.8 Sistem penyesuaian sakelar deteksi produk
5.9 Kotak kontrol listrik stainless steel, tombol tahan air, tombol berhenti darurat
4.Karakteristik Kinerja
1. Sensor fotoelektrik secara otomatis mendeteksi masuknya botol dan label diberi makan secara otomatis.
2. Roll penggerak label secara otomatis memberi makan label melalui encoder dan sinyal fotoelektrik, dan label selalu berada dalam keadaan diperketat.
3. Peralatan ini sepenuhnya otomatis dan tidak memerlukan perhatian khusus.
4. Dilengkapi dengan fungsi deteksi label dan memiliki fungsi alarm ketika gulungan label habis.
5. Sensor deteksi produk menggunakan mata listrik berkecepatan tinggi SICK dari Jerman.
6. Memiliki rangka penyesuaian sensor deteksi produk untuk mewujudkan penyesuaian cepat titik deteksi.
7. Memotong label sebelumnya menggunakan pemotong tunggal atau ganda, mentransfer label ke posisi pra-labeling melalui drum vakum, lalu menempelkan label. Label ditempelkan dengan halus pada permukaan botol.
8. Sistem pemberian makan menggunakan metode pemberian makan terus-menerus untuk mencapai proses labeling yang lebih cepat dan stabil.
9. Seluruh mesin menggunakan sistem pelumasan minyak cerdas, yang membuat transmisi lebih efisien dan bagian transmisi seperti bearing memiliki umur pemakaian yang lebih lama.
10. Kerangka mesin keseluruhan terbuat dari stainless steel dengan tampilan yang bersih dan tahan lama.
11. Baut dan roda bintang mulut botol mengadopsi konsep perakitan cepat, yang secara efektif mengurangi waktu yang dihabiskan untuk pergantian jenis botol.
Kerangka & Tampilan:
Kerangka bearing menggunakan cat baja karbon berkualitas tinggi untuk pencegahan karat dan umur pemakaian yang panjang. Bagian lainnya terbuat dari stainless steel 304.
Lemari kontrol listrik mandiri:
Tahan air, tahan kelembapan, tahan debu, dan juga dilengkapi dengan pendingin udara mandiri untuk dissipasi panas, sehingga dapat beradaptasi dengan lebih banyak lingkungan kerja serta melindungi peralatan dengan lebih baik dan memastikan keamanan listrik.
Stasiun penempelan lem panas:
1. Mesin ini menggunakan motor servo independen untuk membuka label, korektor deviasi otomatis dan roller servo independen bekerja sama untuk memberi makan label dan menjaga akurasi pemotongan dalam 1mm. Drum hisap vakum label dikontrol oleh motor servo independen, dan sistem perekat yang dikembangkan sendiri serta drum vakum bekerja sempurna bersama-sama untuk memastikan akurasi penempelan label, serta operasi pengangkatan listrik yang praktis dan menghemat waktu.
2. Peralatan beroperasi dalam mode otomatis. Inverter frekuensi menyesuaikan kecepatan sesuai dengan jumlah botol, dan pengaturan default adalah tidak menempelkan label jika tidak ada botol, tidak menggunakan perekat jika tidak ada label.
Korektor deviasi:
Korektor deviasi otomatis bekerja dengan roller label servo independen untuk menjaga akurasi penempelan label dalam 0,3mm, dan sudut kemiringan label kurang dari 1°, memastikan stabilitas pemotongan label.
Drum pemotong vakum:
Pisau pemotong menggunakan bahan khusus dari Jerman, yang sangat tahan lama dan tahan aus. Selain itu, kami merupakan yang pertama di China yang menerapkan fungsi pendinginan suhu konstan sehingga pisau dapat beroperasi pada kecepatan tinggi tanpa panas, untuk memperpanjang masa pakai. Ini juga memastikan bahwa tingkat kegagalan penempelan label dijaga di bawah 1/10.000.
Drum hisap label vakum dan blok hisap:
Dikendalikan oleh motor servo independen, drum vakum dan drum pemotong berkoordinasi dengan lancar selama transisi. Desain sirkuit vakum internal canggih pada drum memastikan hisapan label stabil dan menghilangkan fenomena label jatuh. Dilengkapi juga dengan fungsi deteksi label. Jika label terlepas, sistem akan memberi peringatan dan mati.
Blok sedotan satu bagian memiliki presisi tinggi dan sepenuhnya memecahkan masalah akurasi jahitan yang buruk. Ini memiliki ketebalan yang baik dan bahkan aplikasi lem. Permukaan khusus diobati dengan lem anti lengket untuk memecahkan masalah lem residu. Bahan paduan aluminium tahan lama dan hemat biaya, dan efek pelabelan lebih indah.
Rol lem:
Rol jenis sarang lebah digunakan untuk penggulung lem, ketebalan lem dapat disesuaikan, dan jumlah lapisan lem adalah 1,2-1,6 sutra (sekitar 80.000 label / kg).
Teknologi perekat refluks drainase cairan dikembangkan secara independen, tanpa membuang lem dan lem residu. Lem dapat didaur ulang untuk mengurangi biaya, dan sumber panas tanpa kontak di dalam rol dapat secara efektif melindungi label dari terbakar. Selain itu, bantalan tahan panas dan bahan disipasi panas digunakan untuk memastikan operasi yang stabil.
Sistem pemasangan bebas goresan:
Screw pengumpan tradisional yang dapat menggores botol telah diganti dengan sistem pengumpan tanpa goresan.
Perangkat blok:
Ada mata listrik yang terpasang 3 meter sebelum dan sesudah peralatan untuk mendeteksi apakah bahan di lini produksi penuh. Ketika ada kekurangan bahan di bagian depan atau botol tersangkut di bagian belakang, PLC akan segera mengontrol silinder untuk membuka dan menghentikan botol setelah menerima sinyal, dan peralatan akan langsung beroperasi dari kecepatan tinggi ke rendah atau dalam keadaan hibernasi siaga untuk menghemat konsumsi energi peralatan. Ketika sinyal mata listrik diterima lagi, blok silinder akan ditutup. Peralatan akan secara otomatis beroperasi dari kecepatan rendah ke tinggi dan tidak memerlukan operasi manual.
Mekanisme penekanan botol:
Struktur pegas ketegangan tiga tahap digunakan untuk memastikan pengangkatan vertikal, tekanan seragam pada botol, dan stabilitas tinggi. Penyesuaian pengangkatan listrik menghemat tenaga kerja dan waktu.
Cetakan dasar:
1. Mengadopsi struktur perakitan dan pembongkaran cepat untuk mengurangi waktu yang dibutuhkan dalam pergantian jenis botol. Setelah cetakan dasar posisi diperbaiki untuk pertama kalinya, Anda hanya perlu merakitnya secara berurutan tanpa koreksi sekunder.
2. Cetakan dasar dengan jarum pemosisi mekanis berputar sebanyak 3 putaran untuk menemukan slot pemosisian, sehingga dapat mencapai penempelan label titik tetap yang akurat.
Sistem dual antarmuka manusia mesin:
Layar sentuh utama dan sekunder berasal dari merek Schneider. Antarmuka dan parameter di antara keduanya saling terhubung untuk mengontrol peralatan. Layar sentuh sekunder dapat dipindahkan untuk memudahkan penyesuaian dan penggunaan mesin. Personel tidak perlu bergerak bolak-balik, menghemat waktu penyesuaian mesin.
Sistem pelumasan:
Sistem pelumasan otomatis yang diimpor dari Korea digunakan. Interval waktu pelumasan otomatis dapat diatur pada layar sentuh, yang memainkan peran pemeliharaan yang baik pada peralatan dan memperpanjang umur pemakaian peralatan.
5.SKeselamatangjaminan
Tombol berhenti darurat, kabinet listrik dengan fungsi tahan air
Spesifikasi desain untuk sistem pasokan dan distribusi listrik (GB50052-95)
Spesifikasi desain distribusi tegangan rendah (GB50054-95)
Kode untuk konstruksi dan penerimaan instalasi peralatan pengangkutan kontinu (GB50270-38)
RIS 10 keselamatan mesin
RIS 15 perlindungan bagi bagian bergerak perangkat
Faktor risiko untuk berhenti mendadak RIS 58
Spesifikasi kabel daya: 0.5 X5 inti kabel pelindung RV, tegangan sistem: 220V daya 2KW
Kabel pipa PVC
Kotak sakelar tahan air tertutup penuh
terminal phoenix
Kode untuk konstruksi dan penerimaan instalasi peralatan pengangkutan kontinu (GB50270-38)
Instalasi yang baik, operasi mekanis dan listrik
Hasil laporan penerimaan statis dan dinamis
Parameter Teknis
Jumlah stasiun kerjaS:12 |
Sumber Daya:AC380V 50Hz20kW |
Kapasitas:12000-15000BPH (tergantung pada bentuk botol dan label) |
Metode penyesuaian kecepatan:kecepatan variabel terus-menerus |
Ketepatan penandaan: ±1.5mm(kesalahan ukuran botol dalam ±0.3mm) |
Diameter botol: ≤φ105mm |
Diameter dalam gulungan label: φ152.4mm |
Diameter luar gulungan label: φ600mm |
Tinggi maksimum label: 130mm |
Tinggi minimum label: 30mm |
Metode perekatan: tempel di kedua ujung setiap label |
Suhu perekatan:120~160℃ |
Bahan label:Opp, Film pearlescent, film komposit kertas plastik, label kertas |
Sumber udara: 5kg |
7.DaftarUtamaElistrikCompokomponen
Item |
Merek |
Asal |
antarmuka manusia mesin 10 inch |
Schneider |
Perancis |
7 inch antarmuka manusia mesin yang dapat digerakkan |
Schneider |
Perancis |
PLC |
Beckhoff |
Jerman |
Motor servo pemberian |
ABB |
Swiss |
Driver servo pemberi umpan |
ABB |
Swiss |
Servo motor |
Inovasi |
China |
Servo drive |
Inovasi |
China |
Modul Ekspansi Keseluruhan |
Inovasi |
China |
Modul kontrol suhu |
Inovasi |
China |
Sistem koreksi dan panduan deviasi |
TECHMACH |
China |
Inverter |
Danfoss |
Denmark |
Sensor Botol |
Sakit |
Jerman |
LABEL SENSOR |
Sakit |
Jerman |
Kontak AC |
Schneider |
Perancis |
Relay |
Schneider |
Perancis |
pemindahan sumber daya |
MeanWell |
TAIWAN |
Silinder |
AIRTAC |
TAIWAN |
Motor pompa lem |
SPG |
Korea Selatan |
Pemutus |
Schneider |
Perancis |
saklar darurat |
Schneider |
Perancis |
Motor utama |
Siemens |
Jerman |
8.BagianSdariCdioperasikanCklien